Typical cars include 30,000 components, including fasteners, from dozens of manufacturers. These parts must arrive at an OEM’s assembly facility in order and at the proper time. A huge task.
It’s so big that many OEMs use logistics businesses to receive supplier parts and sequence them by customer order.
Princeton-based Diversity Vuteq is one. Diversity Vuteq’s booming operation delivers 6,500 components daily to Princeton’s Toyota assembly plant, which makes the Sienna minivan and Highlander SUV. Diversity Vuteq supplies Toyota with injection-molded plastic parts and logistics.
Princeton-based Diversity Vuteq is one. Diversity Vuteq’s booming operation delivers 6,500 components daily to Princeton’s Toyota assembly plant, which makes the Sienna minivan and Highlander SUV. Diversity Vuteq supplies Toyota with injection-molded plastic parts and logistics.
“We are a just-in-time supplier and constantly move a high volume of automotive components of all shapes and sizes, from parts that go under the hood to under the body,” explains Diversity Vuteq manufacturing and logistics manager Nathan Stone.
UNEX Manufacturing Inc.’s heavy-duty, galvanized steel rollers move empty and full totes throughout 38 bays each shift. Carton flow was not always continuous.
Stone and his crew realized the carton flow area needed a big update some years ago. Components changed, making bags larger and heavier. To meet automobile industry expectations, major adjustments were needed.
We had narrow tracks and rollers. Wheels broke. Shafts and bearings littered the floor. Totes hung. Stone claims team members were climbing inside the lane to pull out totes, which was unsafe. Since components are continually changing, we required a drop-in solution that was robust, efficient, and safe.
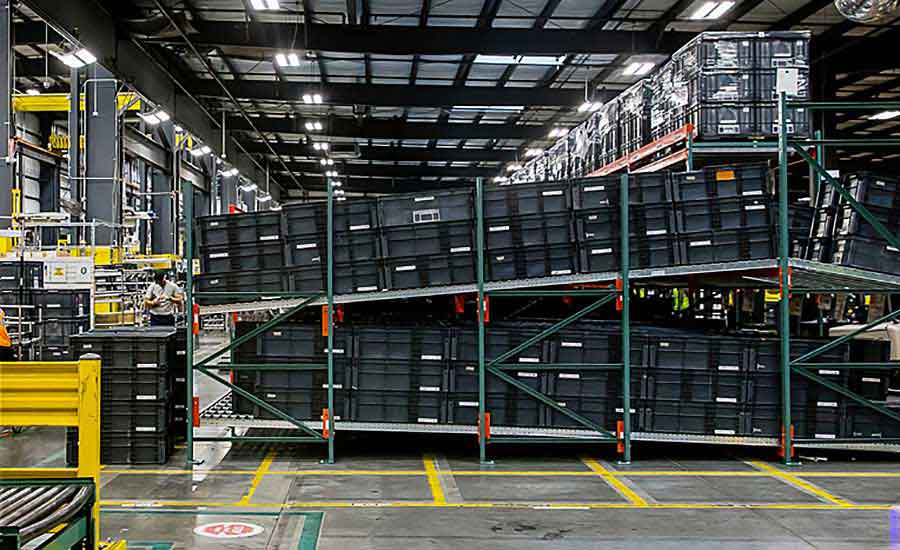
Stone worked with Darrin Wicks, a material handling specialist at St. Louis-based Indoff Corp., to develop a new carton flow area that would serve the plant for years to come. In several instances, Indoff has helped companies enhance their processes with UNEX.
Building, Line, Electricity
Wicks explains, “We modified the entire system to give the plant the flexibility to put heavy and large containers, as well as small, light ones, onto the racks. “UNEX heavy duty rollers offered the versatility and durability we needed.”
The team tested some lanes. Wicks claims they rolled well.
After the rollers were successful, the crew added 652 heavy-duty SpanTrack steel roller lanes over 38 bays. To prevent downtime at the busy factory, the installation was performed in one week during the usual closure.
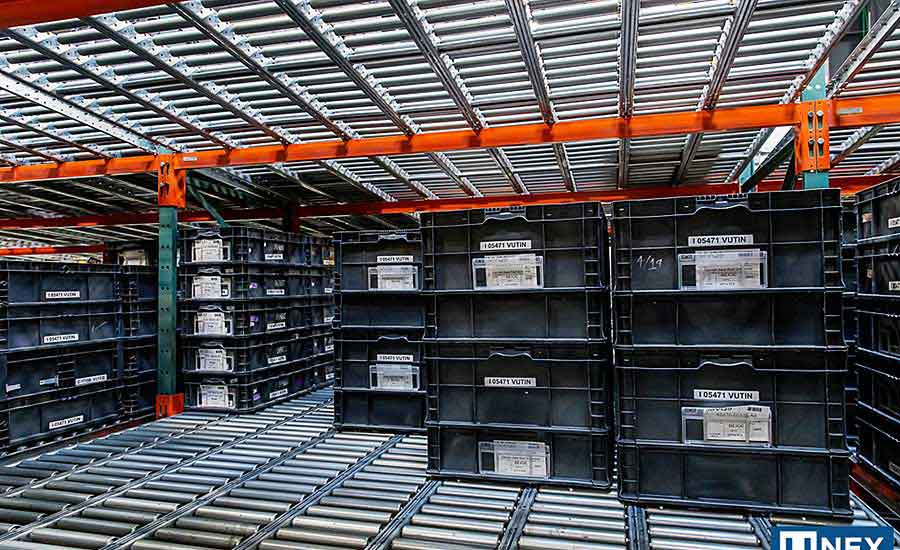
This project was huge. Stone said they updated their storage system. “With the old system, I had to change finished goods and conveyor beds. Just relocate my signs and containers. Moving goods and entering lanes is easy.”
Knuckles Needed
The facility fills automotive requests with totes of parts. Empty totes are collected, replenished with components, and returned to the top level. “The lanes with the newly filled totes are pitched, so height can be an ergonomic issue if our team members have to lift them too high and push them toward production,” explains Stone.
UNEX added knuckles at rear-loading zones to reduce over-the-shoulder lifting and improve tote movement along the lane. Attachments bend the track, lowering the pick point. “We typically use the knuckles with light duty rollers,” explains UNEX central east sales manager Ryan McKinney. “For this project, we customized the heavy duty roller knuckles to make it easy for workers to load totes and meet the customer’s ergonomic standards.”
The old rollers “were just not made for the abuse of a high volume of totes moving forward on a daily basis,” Stone remembers. Tough UNEX rollers. No repairs needed. Solid frames.”
All-steel, full-width rollers with ball bearings reduce slope and maximize carton support. They straighten boxes and bins.
Wicks recommends UNEX steel rollers for weight concerns. “These are plant workhorses.”
UNEX racks uniformly clean the plant. “No gaps. Everything fits. “Much cleaner,” says Stone. “People are impressed.”
The plant’s heavy-duty SpanTrack steel rollers had worked effectively for months. Stone also values another benefit. “The steel roller lanes make my team and me worry less. Modern labor is scarce. If I can reduce team headaches, they’ll stay longer and be happier.”